Table Of Content
- Avoiding Sinks With Proper Venting
- A Comprehensive Guide to Injection Molding Design for Optimal Manufacturing
- The Significance of Design for Manufacturability (DFM) in Mold Production
- Injection Molding Basics: An Introduction to Designing Molded Parts
- CNC Machining Surface Finishes: Choosing the Best Option for CNC Machined Parts

Quality articles for engineers and designers to learn about Digital Manufacturing. This way design errors can be identified early, while the cost of change is still low. Finishes are usually applied to the mold by hand, which can be an expensive process, especially for high-grade finishes. If your part is not for cosmetic use, don’t apply a costly high-grade finish. Here we collected some tips to help you minimize the cost of your Injection molded project. High-performance engineering thermoplastic with excellent strength and thermal & chemical resistance.
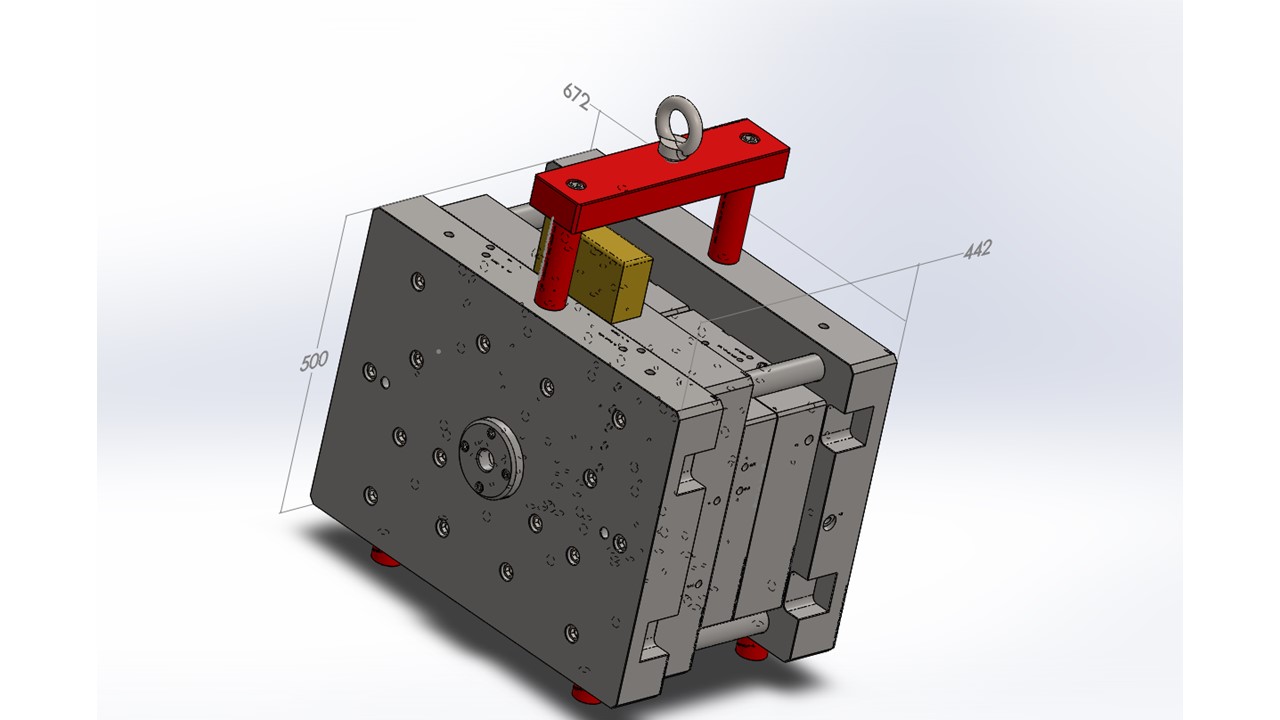
Avoiding Sinks With Proper Venting
Side-action cores and the other in-mold mechanisms can increase the cost of tooling by 15% to 30%. This translates to a minimum additional cost for tooling of approximately $1,000 to $1,500. The purpose of the injection unit is to melt the raw plastic and guide it into the mold.
Registration Open for UMass Lowell Plastics Engineering Seminars - PlasticsToday
Registration Open for UMass Lowell Plastics Engineering Seminars.
Posted: Wed, 29 Nov 2023 11:43:17 GMT [source]
A Comprehensive Guide to Injection Molding Design for Optimal Manufacturing
If you only require a few thousand parts, then this would be your final production step. With the design finalized, it time to get started with Injection molding with a small pilot run. The Society of Plastics Industry (SPI) explains several standard finishing procedures that result in different part surface finishes. Engineering thermoplastic with high strength, stiffness & moisture resistance and self-lubricating properties. Blend of two thermoplastics resulting in high impact strength, excellent thermal stability, and high stiffness.
The Significance of Design for Manufacturability (DFM) in Mold Production
Sometimes referred to as a press, an injection molding machine produces products, tools, or equipment. The majority of these machines are used for plastic injection molding. An injection mold is the tooling machinery used to create components or products.
The mold halves then separate and the finished part gets ejected out before the tool closes again for the next cycle. Designing injection molded parts requires consideration of numerous variables that can significantly impact the functionality and quality of the final product. Common issues that may arise during the injection molding process include sink marks, flow lines, warping, and more. Therefore, having a thorough understanding of the injection molding design guide is essential to achieving outstanding results.
Once the design specifications are established, the next step is to select the appropriate mold material. The choice of material depends on various factors such as cost, durability, and specific application requirements. Common materials used for injection molds include steel and aluminum alloys. Each material has its advantages and considerations, so it’s crucial to consult with experts or experienced manufacturers to make an informed decision. Wall thickness is a critical dimension that affects both manufacturability and functionality.
This molder speaks the language of medicine - PlasticsToday
This molder speaks the language of medicine.
Posted: Fri, 01 Dec 2023 01:10:22 GMT [source]
How to design and build a plastic injection mold
A good rule of thumb is to apply 1 degree of draft per 1 inch of cavity depth, but that still may not be sufficient depending on the material selected and the mold's capabilities. Protolabs uses CNC milling to manufacture the majority of the features in the mold. The result of our manufacturing process drives a unique wall thickness and draft angle based on the end mill that we are using for each feature. This is where our design for manufacturability (DFM) analysis becomes particularly helpful as our software looks at each part feature separately and compares it to our toolset. The design analysis highlights the part geometry where increased draft and thickness may be required. RapidDirect offers outstanding injection mold tooling services to improve the molding process and the quality of molded parts.
Injection Molding Basics: An Introduction to Designing Molded Parts
It results in a visible seam or gap along the parting line of the molded part. Deflection occurs when the molded part warps or bends out of its intended shape during cooling. Both defects can result in parts not meeting the required specifications, leading to increased scrap rates and reduced productivity. These air trap defects are among the most critical flaws in injection molding. Likewise, if the air originally within the mold gets hot and compressed tight enough, it can explode, destroying both the molded component and the mold. Quality control and inspection aim to guarantee that the molded parts meet the quality and performance requirements.
CNC Machining Surface Finishes: Choosing the Best Option for CNC Machined Parts
Although these defects do not usually impact the integrity of parts, they become a severe problem when it burns the molded component such that it causes degradation. If you want to produce high-quality machined parts with a sleek appearance, it’s essential to consider some critical factors related to CNC machining. No one ever said that designing and manufacturing molded parts was easy.
Gate location is critical to virtually every attribute of an injection molded part. It affects appearance, warpage, tolerances, surface finish, wall thickness, molded in stresses and physical properties, to name a few. There are tens of thousands of different materials available for injection molding. Most polymers may be used, including all thermoplastics (such as nylon, polyethylene, and polystyrene) and some elastomers.
So why shouldn’t you take advantage of someone else’s years of effort? You can propel yourself forward in a fraction of the time, using Bob’s hard won expertise in areas such as runners, gates, shrinkage, cooling and more. I’ve used hundreds of mold designs since I started in the industry in 1978. And it’s never failed to surprise me how much money I’ve been leaving on the table by not starting off with a proper design.
So, be cautious when using this for highly cosmetic parts that have texture or a high polish. Some are first prototyped through 3D printing where moldability considerations are of limited concern. Others take a more traditional machining route that allows for iterative testing in engineering-grade materials similar to that of molding.
Products can be produced using injection molding techniques in a short space of time for a relatively low cost when compared to other methods, such as 3D printing, for example. The low cost per unit and rapid rate of production that injection molding enables cannot be achieved with any other manufacturing process. Injection molding enables manufacturers to produce high volumes of products or components that are all uniform in shape.
First and foremost, it is important to carefully analyze the material properties that will be used for injection molding. Different materials have varying flow characteristics and shrinkage rates, which can greatly affect the final product. Understanding these properties will enable you to make informed decisions during the design process. When it comes to injection mold design, achieving optimal design conditions is crucial for the success of the manufacturing process.
After selecting the mold material, the next phase involves designing the mold cavity. This entails creating precise 3D models using computer-aided design (CAD) software. The design should consider factors such as draft angles, gating systems, cooling channels, ejection mechanisms, and parting lines. Lastly, incorporating features such as ribs, reinforcing gussets, or fillets can enhance part strength and rigidity while minimizing material usage.
As the molecules are pushed through each feature, they are forced to bend, turn and distort to form the shape of the part. Turning hard or sharp corners exerts more stress on the molecules than taking gentle turns with generous radii. Abrupt transitions from one feature to another are also difficult for the molecules to fill and form to.
No comments:
Post a Comment