Table Of Content
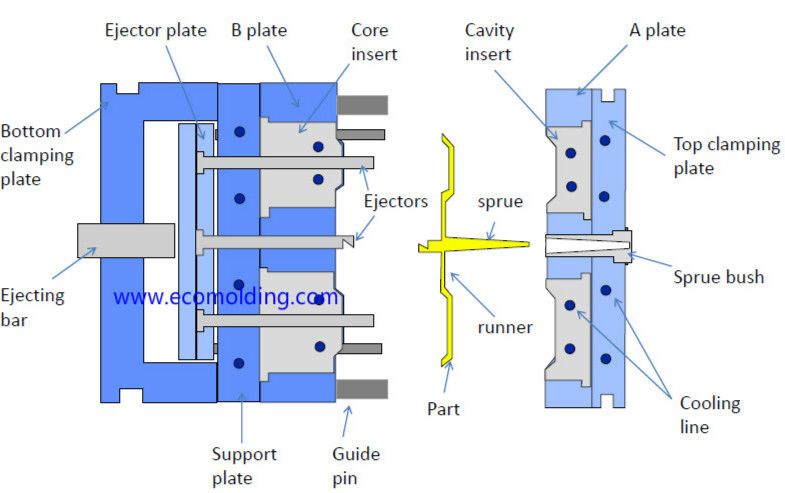
The minimum wall thickness that can be used depends on the size and geometry of the part, structural requirements, and flow behavior of the resin. The wall thicknesses of an injection molded part generally range from 2mm – 4mm (0.080" – 0.160"). Thin wall injection molding can produce walls as thin as 0.5mm (0.020").
Reduce mold and tool design times by 75%
However, it would be best to do this in the final stages of design to minimize complexity. Surface finishes can be used to give an injection molded part a certain look or feel. Besides cosmetic purposes surface finishes can also serve technical needs. Once the mold is manufactured, these complex parts can be reproduced at a very low cost. But changes to the mold design at later stages of development can be very expensive, so achieving the best results on the first time is essential. Follow the guidelines below to avoid the most common defects in injection molding.
Reduce mold production lead times by 80%
Medtech Contract Manufacturer Arterex Acquires Micromold - PlasticsToday
Medtech Contract Manufacturer Arterex Acquires Micromold.
Posted: Tue, 23 Jan 2024 08:00:00 GMT [source]
This is either because the mold cannot be CNC machined or because the material is in the way of ejecting the part. Injection molding is an established manufacturing technology with a long history, but it’s constantly being refined and improved with new technological advancements. Side-action cores are moving elements that enter the mold from the top or the bottom and are used to manufacture parts with overhangs (for example, a cavity or a hole). Side-actions should be used sparingly though, as the cost increases rapidly.

Decoding Part Design in Injection Molding
Thinner walls use less material which reduces cost and take less time to cool, reducing cycle time. The sequence of events during the injection molding of a plastic part is called the injection molding cycle. The cycle begins when the mold closes, followed by the injection of the polymer into the mold cavity.
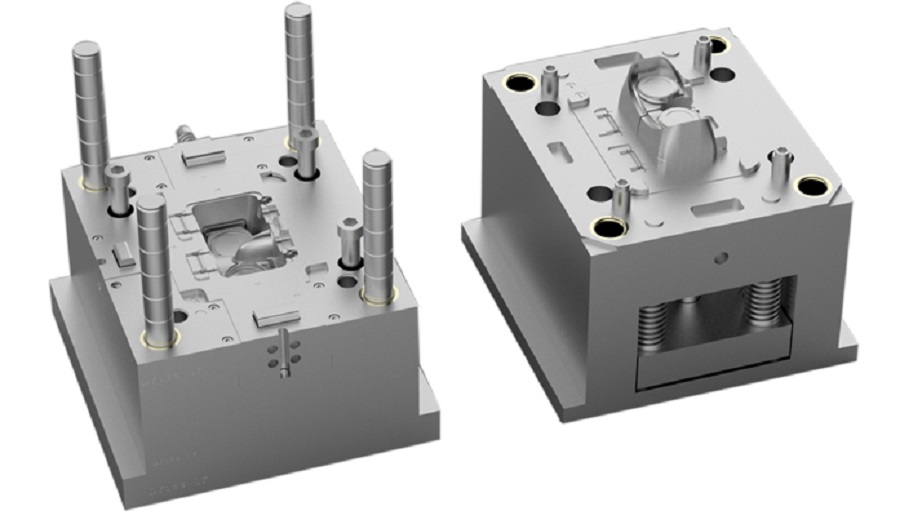
Molds are clamped to the platen of the molding machine, where plastic is injected into the mold through the sprue orifice. Presses are rated by tonnage, which is the calculation of the amount of clamping force that the machine can exert. This force keeps the mold closed during the injection molding process. Tonnage can vary from less than 5 tons to 6,000 tons, although higher tonnage presses are rarely used.
By Design: Polypropylene part design, Part 2 – Living hinges - PlasticsToday
By Design: Polypropylene part design, Part 2 – Living hinges.
Posted: Thu, 30 Nov 2023 15:26:48 GMT [source]
Designers also need to consider gate location because gates leave plastic protruding from the part’s surface. This extra plastic gets trimmed, but it’s best to put gates where any small marks that are left behind are least noticeable. Gates are openings in an injection mold that allow molten plastic to enter the cavity. Sometimes, the parting line is right down the middle of the injected molded part.
Unnecessary thickness can alter part dimensions, reduce strength, and necessitate post-process machining. After you’ve approved your part samples, injection molding production can begin. Depending on the tool’s construction, you can get tens, hundreds, or many thousands of parts.
The assembly process requires meticulous attention to detail as even the slightest misalignment can result in defective or unreliable molds. Once the mold cavity design is complete, it’s time for prototyping and testing. This step helps identify any potential issues or flaws in the mold design before full-scale production. Prototyping involves creating a small number of test samples using the designed mold and evaluating their quality, dimensional accuracy, and functionality. Additionally, wall thickness uniformity plays a significant role in achieving desirable outcomes. Uneven wall thickness can result in variations in cooling rates and eventual warping or sink marks on the finished product.
The Pros and Cons of Injection Molding
By considering the various components, steps, and review criteria outlined in this article, mold designers can create molds that produce high-quality plastic products consistently. An effective mold design ensures smoother production processes, reduces waste, and contributes to overall cost-effectiveness in the injection molding industry. To improve the efficiency and quality of the injection molding process, designers and engineers should aim for rounded features rather than sharp corners and edges.
I really like this tutorial, there is so much good information inside! NMG has more than 85 years of experience partnering with organizations to bring their industrial, IoT, lighting, medical, telecommunications, consumer, and aerospace products to life. We solve your most complex challenges in engineering design, manufacturing, and supply chain management. External undercuts are the easiest and most cost effective as we accommodate through pin-actuated side-actions.
An ejection system is used to push the molded part out of the clamping unit. A mold release agent may be sprayed onto the surface of the mold cavity before injection to facilitate easy ejection and prevent damage to the new part. Sharp corners have high-stress concentration and plastic flow is hindered. Rounded corners have reduced-stress concentrations and plastic flow is enhanced. Burn marks as black rust-colored marks on the surface or edges of the molded component.
The direct or sprue gate is a manually trimmed gate that is used for single cavity molds of large cylindrical parts that require symmetrical filling. Direct gates are the easiest to design and have low cost and maintenance requirements. Direct gated parts are typically less stressed and provide high strength. With injection molding, granular plastic is fed by gravity from a hopper into a heated barrel.
No comments:
Post a Comment